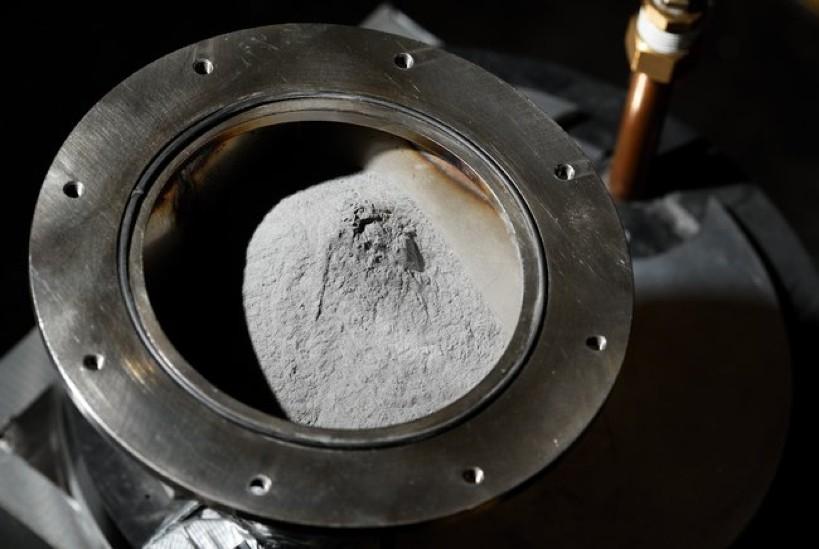
Futuro en po
A empresa sueca VBN Components produce produtos siderúrxicos mediante tecnoloxías aditivas utilizando po con aditivos, principalmente ferramentas como brocas e fresas. A tecnoloxía de impresión 3D elimina a necesidade de forxa e mecanizado, reduce o consumo de materias primas e ofrece aos usuarios finais unha variedade máis ampla de materiais de alta calidade.
A oferta de compoñentes VBN inclúe, por exemplo. Vibenita 290que, segundo a compañía sueca, é o aceiro máis duro do mundo (72 HRC). O proceso de creación de Vibenite 290 consiste en aumentar gradualmente a dureza dos materiais ata. Unha vez que se imprimen as pezas desexadas a partir desta materia prima, non se precisa ningún outro procesamento que non sexa a moenda ou a electroerosión. Non é necesario cortar, fresar ou perforar. Así, a empresa crea pezas con dimensións de ata 200 x 200 x 380 mm, cuxa xeometría non se pode producir mediante outras tecnoloxías de fabricación.
O aceiro non sempre é necesario. Un equipo de investigación de HRL Laboratories desenvolveu unha solución de impresión 3D. aliaxes de aluminio con alta resistencia. Chámase método nanofuncional. En pocas palabras, a nova técnica consiste na aplicación de pos nanofuncionais especiais a unha impresora 3D, que despois son "sinterizados" cun láser en capas finas, o que leva ao crecemento dun obxecto tridimensional. Durante a fusión e a solidificación, as estruturas resultantes non se destrúen e manteñen toda a súa resistencia debido a que as nanopartículas actúan como centros de nucleación para a microestrutura prevista da aliaxe.
As aliaxes de alta resistencia como o aluminio utilízanse amplamente na industria pesada, na tecnoloxía da aviación (por exemplo, na fuselaxe) e nas pezas de automóbiles. A nova tecnoloxía de nanofuncionalización dálles non só unha alta resistencia, senón tamén unha variedade de formas e tamaños.
Suma en vez de resta
Nos métodos tradicionais de traballo do metal, o material de refugallo é eliminado por mecanizado. O proceso aditivo funciona á inversa: consiste en aplicar e engadir capas sucesivas dunha pequena cantidade de material, creando pezas XNUMXD de case calquera forma baseadas nun modelo dixital.
Aínda que esta técnica xa é moi utilizada tanto para a creación de prototipos como para a fundición de modelos, o seu uso directamente na produción de bens ou dispositivos destinados ao mercado resultou difícil debido á baixa eficiencia e ás propiedades do material pouco satisfactorias. Porén, esta situación está cambiando aos poucos grazas ao traballo de investigadores de moitos centros de todo o mundo.
A través dunha minuciosa experimentación, melloráronse as dúas tecnoloxías principais da impresión XNUMXD: deposición láser de metal (LMD) i fusión selectiva por láser (ULM). A tecnoloxía láser permite crear detalles finos con precisión e obter unha boa calidade de superficie, o que non é posible coa impresión de feixe de electróns 50D (EBM). En SLM, o punto do feixe láser diríxese sobre o po do material, soldándoo localmente segundo un patrón determinado cunha precisión de 250 a 3 micras. Pola súa banda, LMD utiliza un láser para procesar o po para crear estruturas XNUMXD autoportantes.
Estes métodos resultaron moi prometedores para crear pezas de avións. e, en particular, a aplicación da deposición láser de metal amplía as posibilidades de deseño de compoñentes aeroespaciais. Poden estar feitos de materiais con estruturas internas complexas e gradientes que non eran posibles no pasado. Ademais, ambas as tecnoloxías láser permiten crear produtos de xeometría complexa e obter unha funcionalidade estendida de produtos dunha ampla gama de aliaxes.
En setembro pasado, Airbus anunciou que equipara o seu A350 XWB de produción cunha impresión aditiva. soporte de titanio, fabricado por Arconic. Este non é o final, porque o contrato de Arconic con Airbus prevé a impresión en 3D a partir de po de titanio e níquel. partes do corpo i sistema de propulsión. Non obstante, hai que ter en conta que Arconic non usa tecnoloxía láser, senón a súa propia versión mellorada do arco electrónico EBM.
É probable que un dos fitos no desenvolvemento de tecnoloxías aditivas no traballo metalúrxico sexa o primeiro prototipo presentado na sede do grupo holandés Damen Shipyards no outono de 2017. hélice de barco aliaxe metálica que leva o nome VAAMpeller. Despois das probas adecuadas, a maioría das cales xa se realizaron, o modelo ten a posibilidade de ser aprobado para o seu uso a bordo dos buques.
Dado que o futuro da tecnoloxía metalúrxica reside nos pos de aceiro inoxidable ou en compoñentes de aliaxe, paga a pena coñecer aos principais actores deste mercado. Segundo o "Informe de mercado de po de metal de fabricación aditiva" publicado en novembro de 2017, os fabricantes máis importantes de po metálico de impresión 3D son: GKN, Hitachi Chemical, Rio Tinto, ATI Powder Metals, Praxair, Arconic, Sandvik AB, Renishaw, Höganäs AB. , Metaldyne Performance Group, BÖHLER Edelstahl, Carpenter Technology Corporation, Aubert & Duval.
Impresión de hélice WAAMpeller
Fase líquida
As tecnoloxías de aditivos metálicos máis coñecidas actualmente dependen do uso de po (así se crea a citada vibenita) "sinterizados" e fundidos con láser ás altas temperaturas necesarias para o material de partida. Porén, están xurdindo novos conceptos. Investigadores do Laboratorio de Enxeñaría Criobiomédica da Academia Chinesa de Ciencias de Pequín desenvolveron un método Impresión 3D con "tinta", consistente nunha aliaxe metálica cun punto de fusión lixeiramente superior á temperatura ambiente. Nun estudo publicado na revista Science China Technological Sciences, os investigadores Liu Jing e Wang Lei demostran unha técnica para a impresión en fase líquida de aliaxes a base de galio, bismuto ou indio coa adición de nanopartículas.
En comparación cos métodos tradicionais de prototipado de metal, a impresión 3D en fase líquida ten varias vantaxes importantes. En primeiro lugar, pódese conseguir unha taxa relativamente alta de fabricación de estruturas tridimensionais. Ademais, aquí pode axustar de forma máis flexible a temperatura e o fluxo do refrixerante. Ademais, o metal condutor líquido pódese usar en combinación con materiais non metálicos (como os plásticos), o que amplía as posibilidades de deseño de compoñentes complexos.
Científicos da American Northwestern University tamén desenvolveron unha nova técnica de impresión en 3D de metal que é máis barata e menos complexa que a coñecida anteriormente. En lugar de po metálico, láseres ou feixes de electróns, usa forno convencional i material líquido. Ademais, o método funciona ben para unha gran variedade de metais, aliaxes, compostos e óxidos. É semellante ao selo da boquilla tal e como o coñecemos cos plásticos. A "tinta" consiste nun po metálico disolto nunha substancia especial coa adición dun elastómero. No momento da aplicación, está a temperatura ambiente. Despois diso, a capa de material aplicada desde a boquilla sinteriza coas capas anteriores a unha temperatura elevada creada no forno. A técnica descríbese na revista especializada Advanced Functional Materials.
Método de impresión en fase de metal líquido chinés
En 2016, os investigadores de Harvard introduciron outro método que pode crear estruturas metálicas XNUMXD. impreso "no aire". A Universidade de Harvard creou unha impresora 3D que, a diferenza doutras, non crea obxectos capa por capa, senón que crea estruturas complexas "no aire", a partir de metal que se conxela instantáneamente. O dispositivo, desenvolvido na Escola de Enxeñaría e Ciencias Aplicadas John A. Paulson, imprime obxectos utilizando nanopartículas de prata. O láser enfocado quenta o material e fúndeo, creando varias estruturas como unha hélice.
A demanda do mercado de produtos de consumo impresos en 3D de alta precisión, como implantes médicos e pezas de motores de avións, está a crecer rapidamente. E debido a que os datos dos produtos pódense compartir con outros, as empresas de todo o mundo, se teñen acceso ao po metálico e á impresora 3D adecuada, poden traballar para reducir os custos de loxística e de inventario. Como é sabido, as tecnoloxías descritas facilitan moito a fabricación de pezas metálicas de xeometría complexa, por diante das tecnoloxías de produción tradicionais. É probable que o desenvolvemento de aplicacións especializadas supoña prezos máis baixos e apertura ao uso da impresión 3D tamén en aplicacións convencionais.
O aceiro sueco máis duro para impresión 3D:
O aceiro máis duro do mundo - fabricado en Uppsala, Suecia
Película de aluminio para impresión:
Avance na metalurxia: impresión 3D de aluminio de alta resistencia

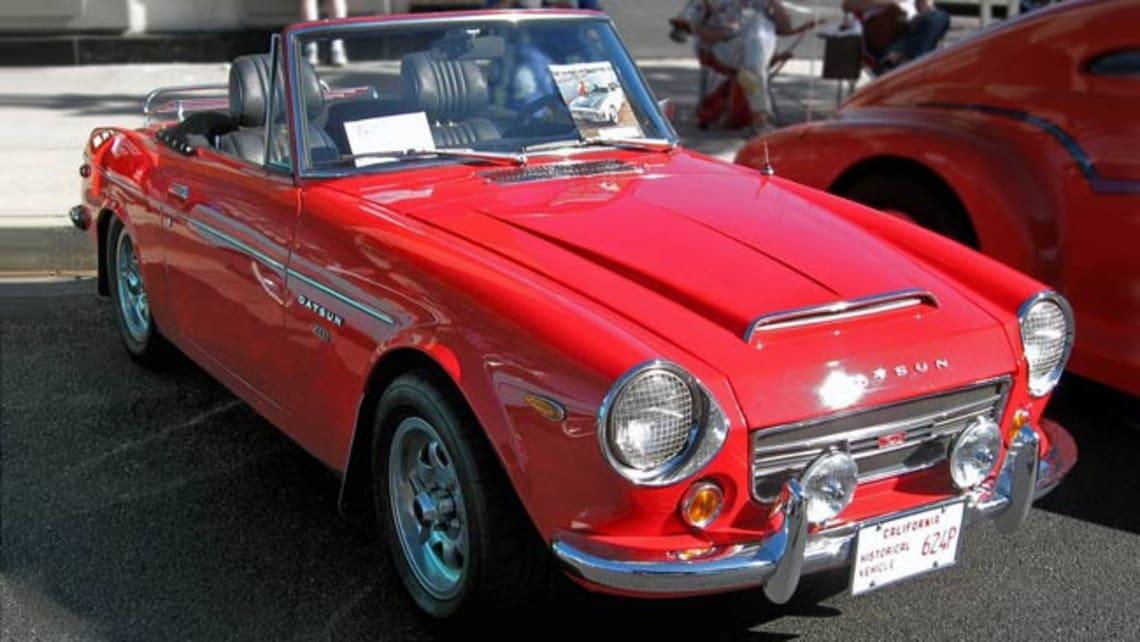
Un comentario
Anónimo
divertido